Manufacturing Orders
ProcessForce manufacturing orders are generated in numerous ways to cater for different production methods and processes. Fundamentally they are used to plan, execute and record production activities.
- Order dependent Bill of Material and Routing - allows for the modification of the product structure and production process to manage every day changes that may occur within production rather than changing company standards
- Method of creation - manually, via MRP based on Sales and/or Forecasts, and Sales Order back-to-back
- Demand Allocation - link multiple Sales Orders to production supply orders
- Dates - enter the required, planned start and planned end dates
- Schedule - forward or backwards to calculate the planned start or planned end date.
- Warehouse - the default warehouse where production will occur
- Planned vs Actual Quantity - monitor the order and item quantity status
- Material Shortage - check available and shortages of stock within planned warehouse and across all warehouses
- Traceability - review all the documents associated with picking and receiving inventory
- Issue Type - alter inventory issues methods from manual to back flush and vice versa
- Operation Times - review operation times and overlaps
- Reporting - report on the status change of operations and record actual production time
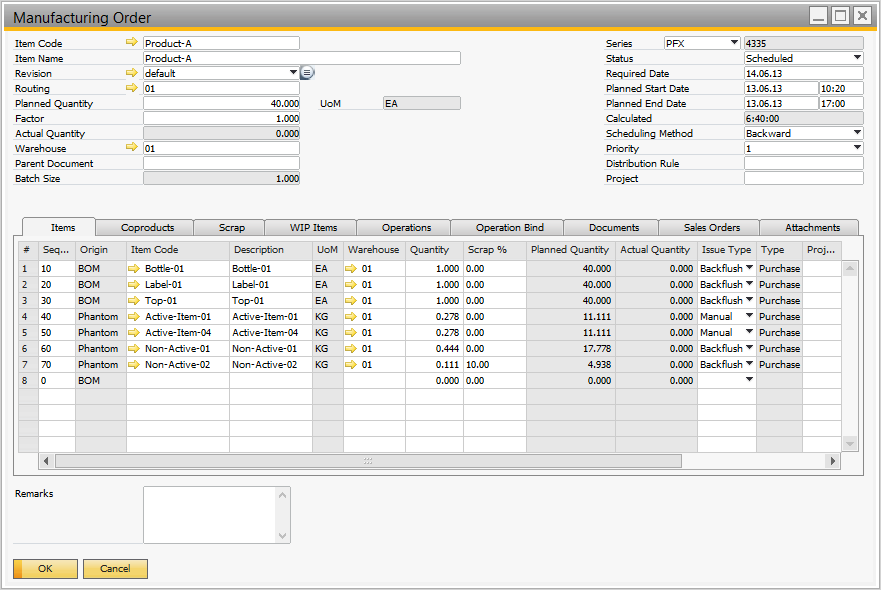